To know the submersible pump can operate, first you have to understand, what is a submersible pump? How does a submersible pump work? The first conclusion is that submersible pumps are not suitable for dry operation. Submersible pumps are designed to work in underwater environments, using an electric motor to rotate the impeller and lift water from low to high. Such pumps are usually designed to operate effectively under water when fully or partially submerged.
If submersible pumps are forced to operate in dry operation, a series of problems may arise.
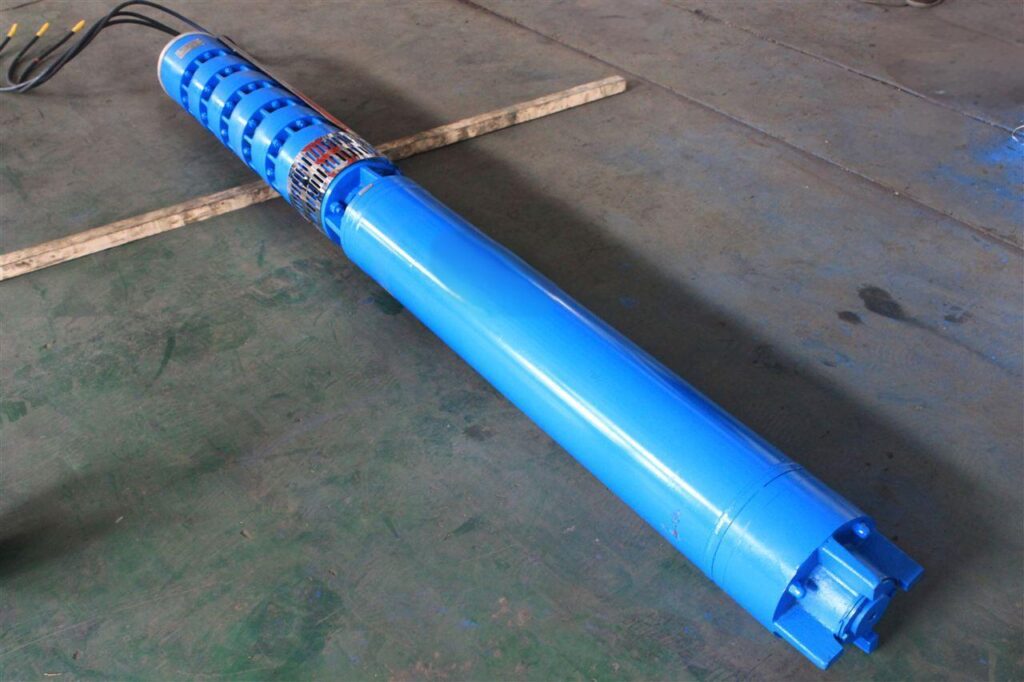
Motor overheating
submersible pump motor will generate a lot of heat during operation. When the pump body is not cooled by water, the heat cannot be effectively dissipated, resulting in overheating of the motor, which may damage the insulation material inside the motor and even cause a fire.
Mechanical seal damage
Submersible pumps usually use mechanical seals to prevent water from entering the motor. In dry operation, the mechanical seal may wear or fail due to lack of lubrication and cooling, further causing water to penetrate the motor and exacerbate motor damage.
Bearing damage
The bearing of the submersible pump needs lubrication and cooling to maintain normal operation. In the dry running state, the bearing may be exacerbated by the lack of lubrication, and even stuck.
Pump body damage
Because submersible pumps are usually designed to work in water, the material and structure of components such as the pump body and impeller may not be suitable for use in dry operation. Long time dry operation may lead to pump body deformation, cracking and other damage.
During the use of submersible pump, in addition to avoiding dry operation, it is necessary to pay attention to the following key points to ensure its normal operation and extend its service life:
Model and specification selection
Meet the demand: pay attention to whether the model and specifications of the submersible pump before use meet their own needs. The size of the submersible pump power is also the focus of purchase.
Motor direction: Familiar with the forward and reverse of the motor when the submersible pump is running. The forward rotation of the motor is the correct way to run the submersible pump, and the reverse transfer for a long time will increase the current and damage the motor.
Installation and protection
Cable protection: When installing the submersible pump, do a good job of protecting the cable, it is strictly prohibited to load the cable or rub it, the cable should be away from the water, and the leakage protection switch should be installed.
Installation environment: When the submersible pump is launched, it should be away from the sand to ensure that the motor has a good heat dissipation space. The submersible pump should be placed upright. During normal drainage, the height of the pump base from the pump pit bottom is not less than 200mm.
Safety standards: the submersible pump must be equipped with a net box to prevent debris from entering the pump body. When laying drainpipes on the same side as the cable, the drainpipe must be 300mm lower than the cable. Do not use pipes smaller than the outlet of the water pump.
Operation and maintenance
Voltage stability: When the submersible pump starts, it is necessary to ensure the stability of the voltage, and avoid starting the pump in the case of abnormal voltage to prevent damage to the motor.
Avoid idling: After starting up, the submersible pump should not be dehydrated and idling, nor can it pump water containing a lot of sediment, otherwise it will burn out the motor and damage the submersible pump.
Regular inspection: Regular inspection and maintenance of the submersible pump and its surrounding environment, and regular lubrication such as butter. The submersible pump in the well that is not used for a long time should be lifted, scrubbed and placed in the indoor ventilated place.
Lubrication and replacement
Oil replacement: After the oil-immersed submersible pump works for a certain period of time (such as 500 hours), the oil in the sealing chamber should be replaced. After working for a year, the oil in the motor cavity should be replaced. Different grades of oil can not be mixed.
Seal inspection: After the submersible pump works for a certain period of time (such as 50 hours), it should check whether the seal is loose or damaged, and tighten or replace the new part in time. After continuous operation of the wet submersible pump for a certain period of time (such as 2000 hours), the lubricating oil needs to be replaced once.
Check the insulation resistance
Insulation resistance test: Use a megohm meter to measure the insulation resistance value of the stator winding of the electric pump to the housing, which is more than 1 megohm (the minimum is not less than 0.5 megohm) can be used, otherwise the winding should be repaired or dried.
Security protection
Protective grounding: The protective grounding of the submersible pump is the requirement of the national mandatory standard, which can ensure the personal safety during use.
Leakage protection: submersible pump should be equipped with leakage protection device to prevent electric shock caused by leakage.
Use precautions
Avoid overload: Avoid using submersible pumps for high load operations for a long time, and observe whether the current value is within the specified range at any time.
Reduce frequent start: the submersible pump can not start too often, because the water in the pipe will return after stopping, and immediately starting may lead to the motor load starting and the current is too large.
In order to ensure the normal operation of the submersible pump and extend its service life, the submersible pump should be avoided in the dry running state. Before use, ensure that the submersible pump is properly installed and fully or partially submerged in water. If the submersible pump needs to be disabled for a long time, it is recommended to remove it from the water and keep it properly to prevent moisture or damage to the motor.