Centrifugal pumps have a simple structure, are easy to manufacture, have a stable flow rate, are highly adaptable, and are easy to operate. They are widely used in a wide range of fields, including shipbuilding, chemical production, municipal life, and so on.
How does a centrifugal pump work?
When a centrifugal pump is working, it relies on the high-speed rotating impeller. The liquid gains energy under the action of inertial centrifugal force and increases the pressure energy. Before the centrifugal pump works, the pump body and the inlet pipeline must be filled with liquid medium to prevent cavitation.
When the impeller rotates rapidly, the blades cause the medium to rotate quickly. The rotating medium flies out of the impeller under the action of centrifugal force. After the water in the pump is thrown out, a vacuum area is formed in the center of the impeller. While continuously sucking in liquid, it continuously gives the sucked liquid a certain amount of energy to discharge the liquid. Centrifugal pumps work continuously in this way.

Main structure of centrifugal pump
Impeller
The impeller is the working part of the centrifugal pump. It relies on its high-speed rotation to work on the liquid to achieve liquid transportation. It is an important part of the centrifugal pump.
The impeller is generally composed of three parts: the impeller, the blades and the cover plate. The cover plate of the impeller is divided into the front cover plate and the rear cover plate. The cover plate on the impeller mouth side is called the front cover plate, and the cover plate on the other side is called the rear cover plate.
The impeller can be divided into the following three types.
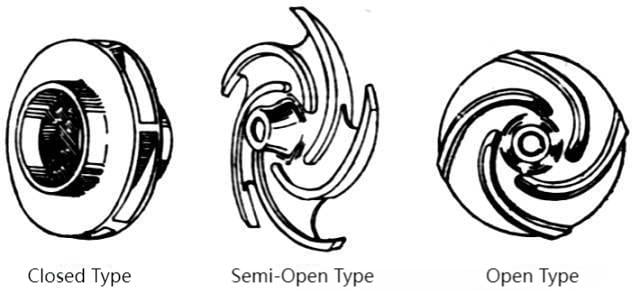
Pump shaft
The main function of the pump shaft of a centrifugal pump is to transmit power and support the impeller to maintain normal operation in the working position. One end of it is connected to the motor shaft through a coupling, and the other end supports the impeller for rotation. The shaft is equipped with bearings, axial seals and other components.
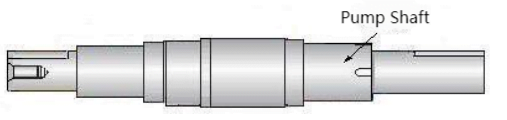
Shaft sleeve
The function of the shaft sleeve is to protect the pump shaft and transform the friction between the packing and the pump shaft into the friction between the packing and the shaft sleeve, so the shaft sleeve is a wearable part of the centrifugal pump.

Bearing
Bearings support the weight and bearing capacity of the rotor. Rolling bearings are mostly used in centrifugal pumps. The outer ring and the bearing seat hole adopt the base shaft system, and the inner ring and the rotating shaft adopt the base hole system. The national standard for matching categories has recommended values, which can be selected according to specific circumstances. Bearings are generally lubricated with grease and lubricating oil.
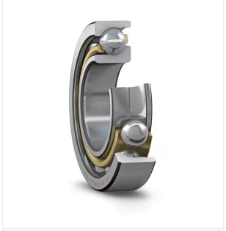
Volute
The volute refers to a spiral flow channel with a gradually increasing cross-sectional area from the impeller outlet to the next-stage impeller inlet or to the pump outlet pipe. Its flow channel gradually expands and the outlet is a diffuser tube. After the liquid flows out of the impeller, its flow rate can be smoothly reduced, so that a large part of the kinetic energy is converted into static pressure energy.
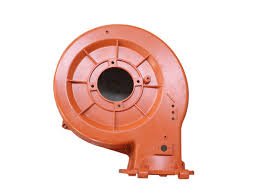
Sealing ring
In order to reduce internal leakage and protect the pump casing, a removable sealing ring is installed on the casing corresponding to the impeller inlet. The radial clearance between the inner hole of the sealing ring and the outer circle of the impeller is generally between 0.1 and 0.2 mm. When the sealing ring is worn, the radial clearance increases, the discharge volume of the pump decreases, and the efficiency decreases. When the sealing clearance exceeds the specified value, it should be replaced in time.
Working process of a centrifugal pump
- Before starting the pump, fill the pump with the liquid to be transported.
- After starting the pump, the pump shaft drives the impeller to rotate at high speed to generate centrifugal force. Under this action, the liquid is thrown from the center of the impeller to the periphery of the impeller, the pressure increases, and it flows into the pump casing at a very high speed (15-25 m/s).
- In the volute pump casing, due to the continuous expansion of the flow channel, the flow rate of the liquid slows down, so that most of the kinetic energy is converted into pressure energy. Finally, the liquid flows into the discharge pipe from the discharge port at a higher static pressure.
- After the liquid in the pump is thrown out, a vacuum is formed in the center of the impeller. Under the pressure difference between the liquid surface pressure (atmospheric pressure) and the pressure in the pump (negative pressure), the liquid enters the pump through the suction pipe and fills the position of the discharged liquid.