Fire pump is a very important part of fire water supply system. When fire occurs, fire pump can quickly provide sufficient water source and water pressure, and control and extinguish the fire. Fire pump needs regular maintenance and fault diagnosis to ensure the normal operation of fire pump. The following are some common faults and maintenance measures.
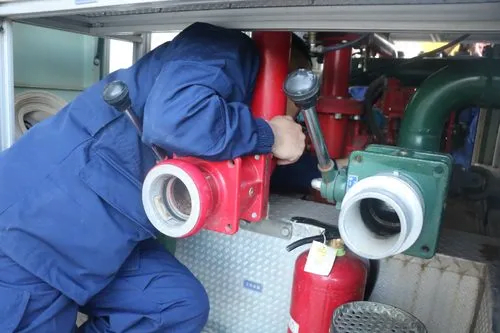
No liquid supply, insufficient liquid supply or insufficient pressure
(1) The pump is not filled with water or not properly vented
Elimination measures: Check whether the pump housing and inlet pipeline are fully filled with liquid.
(2) Speed is too low
Elimination measures: Check whether the motor is correctly wired, whether the voltage is normal or whether the steam pressure of the turbine is normal.
(3) System head is too high
Elimination measures: Check the system head (especially friction loss).
(4) Suction head is too high
Elimination measures: Check the existing net pressure head
(5) Impeller or pipeline is blocked
Elimination measures: Check for obstacles.
(6) Wrong rotation direction
Elimination measures: Check the rotation direction.
(7) Air is generated or there is a leak in the inlet pipeline
Elimination measures: Check the inlet pipeline for cavitation and/or air leakage.
(8) The packing or seal in the stuffing box is worn, allowing air to leak into the pump casing
Elimination measures: Check the packing or seal and replace it as needed, and check whether the lubrication is normal.
(9) Insufficient suction head when pumping hot or volatile liquids
Elimination measures: Increase the suction head and consult the manufacturer.
(10) The foot valve is too small
Elimination measures: Install a foot valve of the correct size.
(11) The bottom valve or inlet pipe is not immersed enough
Action: Consult the manufacturer for the correct immersion depth. Use a baffle to eliminate vortexes.
(12) The impeller clearance is too large
Action: Check whether the clearance is correct
(13) The impeller is damaged
Action: Check the impeller and replace it as required.
(14) The impeller diameter is too small
Action: Consult the manufacturer for the correct impeller diameter.
(15) The pressure gauge is not in the correct position
Action: Check whether the position is correct and check the outlet nozzle or pipe.
The fire pump stops after running for a while
(1) The suction head is too high
Action: Check the existing net pressure head (inlet pipelines that are too small or too long will cause large friction losses).
(2) The impeller or pipeline is blocked
Action: Check for obstructions.
(3) Air is generated or there is a leak in the inlet pipeline
Action: Check the inlet pipeline for cavitation and/or air leaks.
(4) The packing or seal in the stuffing box is worn, allowing air to leak into the pump casing
Action: Check the packing or seal and replace as needed. Check whether lubrication is normal.
(5) Insufficient suction head when pumping hot or volatile liquids
Elimination measures: Increase the suction head and consult the manufacturer.
(6) The immersion depth of the foot valve or inlet pipe is not enough
Elimination measures: Consult the manufacturer for the correct immersion depth and use a baffle to eliminate vortexes.
(7) The pump casing gasket is damaged
Elimination measures: Check the condition of the gasket and replace it as required.
Fire pump power consumption is too high
(1) The rotation direction is incorrect
Elimination measures: Check the rotation direction.
(2) Impeller damage
Elimination measures: Check the impeller and replace it as required.
(3) Rotating parts are stuck
Elimination measures: Check whether the clearance of internal wear parts is normal.
(4) Shaft bending
Elimination measures: Straighten the shaft or replace it as required.
(5) The speed is too high
Elimination measures: Check the winding voltage of the motor or the steam pressure delivered to the turbine.
(6) The head is lower than the rated value. Too much liquid is pumped
Elimination measures: Consult the manufacturer. Install a throttle valve and cut the impeller.
(7) Liquid is heavier than expected
Action: Check specific gravity and viscosity.
(8) Stuffing box is not properly packed
Action: Check packing and repack stuffing box.
(9) Bearing lubrication is incorrect or bearings are worn
Action: Check and replace as required.
(10) Running clearance between wear rings is incorrect
Action: Check whether the clearance is correct. Replace the wear rings of the pump casing and/or impeller as required.
Overheating
(1) Packing or seal in the stuffing box is worn, allowing air to leak into the pump casing
Action: Check packing or seal and replace as required. Check lubrication for normal operation.
(2) Stuffing box is not properly packed (insufficient packing, not properly inserted or run-in, packing too tight)
Action: Check packing and repack stuffing box.
(3) Packing or mechanical seal has design problems
Action: Consult the manufacturer.
(4) Mechanical seal is damaged
Action: Check and replace as required. Consult the manufacturer. (5) Scratched sleeve
Elimination measures: Repair, re-machine or replace as required.
(6) Packing too tight or mechanical seal not adjusted correctly
Elimination measures: Check and adjust packing, replace as required. Adjust mechanical seal (refer to the manufacturer’s instructions provided with the pump or consult the manufacturer).
Rotating parts
(1) Shaft bending
Elimination measures: Straighten the shaft or replace as required.
(2) Incorrect running clearance between wear rings
Elimination measures: Check whether the clearance is correct. Replace the wear rings of the pump casing or impeller as required
(3) Excessive stress on the pipe on the pump casing
Elimination measures: Eliminate stress and consult the manufacturer’s representative. After eliminating stress, check the alignment.
(4) Excessive swing of the shaft or impeller ring
Elimination measures: Check rotating parts and bearings, and replace worn or damaged parts as required.
(5) Dirt between the impeller and the pump casing wear ring, and dirt in the pump casing wear ring
Elimination measures: Clean and inspect the wear ring, and replace as required. Isolate and eliminate the source of dirt.